Navigating the Pottery Creation Journey with JMT Ceramics:
A Guide to Commissions and
Made-To-Order Timelines
​Understanding the intricate process of crafting pottery is key to appreciating the artistry behind each piece at JMT Ceramics. Our commitment to quality and craftsmanship requires time and patience. If you've placed a pre-order with us, here's a helpful guide to shed light on why it may take 6 to 8 weeks for your unique creation to reach you.
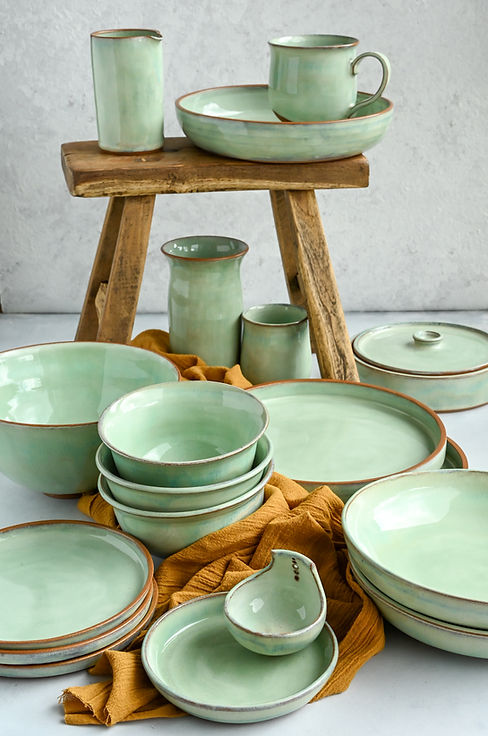
Step One – Design
​
In the vast realm of clay possibilities, choosing a pottery for your home or as gifts can be both exciting and challenging. Whether you're envisioning functional tableware or home decor, the design phase sets the aethestics of your collection.
Consult with us to discuss your ideas - we can advise on clay and glaze pairings to bring your vision to life.
​
For most items, we'll need the size dimensions and a cross-section drawing of your idea (diameter and height) to start with.
Step Two – Shaping the Clay
Working with clay is a dance of precision. Clay's thixotropic nature means it transforms from a wet consistency to a drying state over time. The making process involves preparing clay (wedging) to ensure it's at the right texture for the method of making.
Most of our pieces are thrown on the wheel.
Water is added as the piece is created, with the clay being centered, opened, pulled and shaped. Excess is trimmed off and the piece is carefully removed from the wheel.

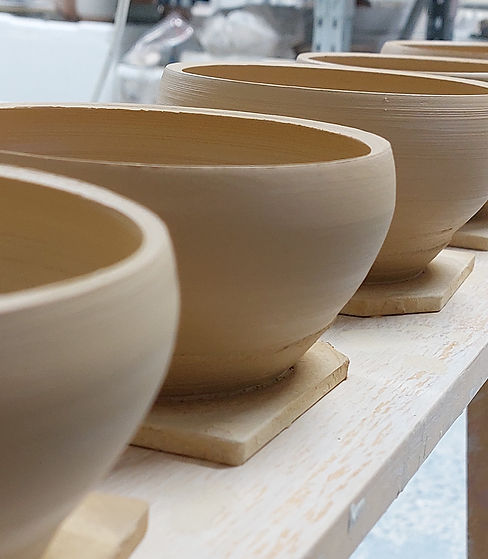
Step Three – Patience in Drying
Drying is a crucial phase where your pottery takes its final form before firing. Depending on your project's size and complexity, the work may be left uncovered in airy spaces or double-bagged to control moisture levels. For the majority of wheel thrown pieces, trimming is required, which means the pots need to achieve 'leather hard' stage, and not beyond.
Factors like weather, humidity, and wind play key roles in the drying process, influencing the overall workflow and timeframes for the whole process.
​
​

Step Four – Precision in Trimming and Cleanup
Once the work is leather hard, it can be trimmed to reveal its final shape and form. This is when footrings are created and all surfaces trimmed and burnished to ensure a smooth finish. This step is vital for preparing your pottery for the bisque firing process.
​
Next the pieces are left to dry slowly till the 'bone dry' phase - especially if there are any joints and attachments, such as handles.


Step Five – Bisque Firing
The bisque firing process involves heating your pottery to 1000°C, burning off water and chemically bound elements. Careful stacking inside the kiln ensures efficient firing, taking approximately 10 hours, followed by a two-day cooling period.
​
The pot is now ready to take on glaze.
Step Six – Artistry in Glazing
Glazing introduces color and character to your creations. The options include oxide washes, underglazes, glazes etc, each requiring a distinct approach.
Glaze chemistry is intricate, involving various metal oxides and fluxes. It's essentially glass. There are many ways to glaze pieces, and a combination of methods may be used to achieve your vision.
This stage is a captivating but time-consuming part of the pottery-making journey. Extra testing may be required to ensure your desired glaze fits with the clay body.


Step Seven – Glaze Firing
The last firing, glaze firing, occurs at 1240°C. This process completes the transformation of your creation into a durable, finished piece. The kiln takes approximately 12 hours to reach temperature and a few days to cool down.
​
Occasionally, a third firing may be necessary for additional decorations such as adding gold accents. Once your pottery has undergone this final stage, it is ready for use.
​
We sand and buff the base of each piece to ensure it is smooth to avoid accidental scratches.
​
Remember, the beauty of your crafted piece reflects the dedication and time invested in its creation. Thank you for choosing JMT Ceramics for your collection!